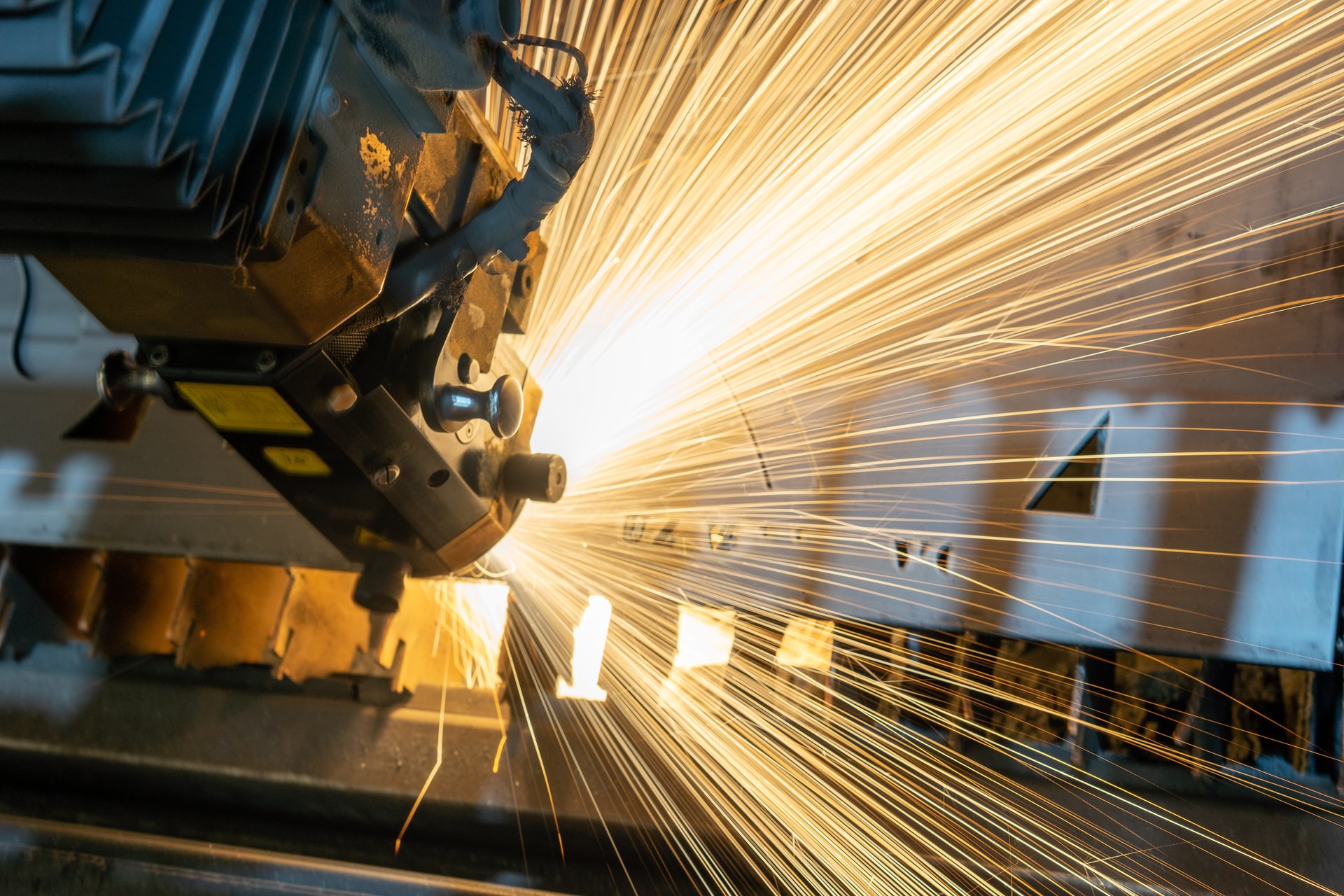
Fujitsu has developed an AI which can highlight abnormalities in the appearance of products to help detect issues earlier.
Catching problems during production enables intervention before materials are wasted—incurring direct and environmental costs. It also saves on the reputational damage and costs associated with returns/recalls after a defective product is shipped to customers.
The solution uses an AI model trained on images of products with abnormalities. These defects are simulated so images of actual products with issues pulled from a production line aren’t necessary.
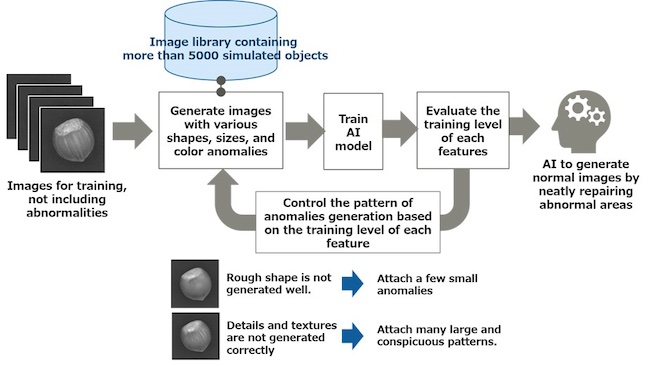
Fujitsu tested its technology at its Nagano Plant, which manufactures electronic equipment, and noted a 25 percent reduction in the man-hours needed for inspecting printed circuit boards.
The AI is able to detect issues like frayed threads or defective wiring patterns – with “world-leading accuracy” – in products that are designed to vary individually; such as different colour carpets or electronics parts with different wiring shapes.
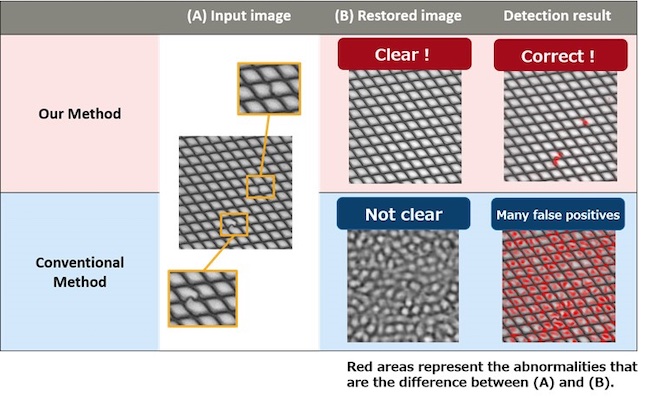
Fujitsu’s AI achieved an AUROC (Area Under the Receiver Operating Characteristics) score in excess of 98 percent when applied to products with variations to their normal appearance.
The Japanese tech giant aims to use its AI advancement for the company’s COLMINA (PDF) brand which aims to deliver digital transformation specifically for the manufacturing industry.
(Photo by Clayton Cardinalli on Unsplash)
Interested in hearing industry leaders discuss subjects like this? Attend the co-located 5G Expo, IoT Tech Expo, Blockchain Expo, AI & Big Data Expo, and Cyber Security & Cloud Expo World Series with upcoming events in Silicon Valley, London, and Amsterdam.